PPS: Produktionsplanung- und Steuerung
Integrieren Sie Ihre Stammdaten, um Ihre Produktion in Echtzeit einfach zu verfolgen.
Das Transfact PPS bietet Ihnen und Ihren Mitarbeitern einen sehr klaren Überblick über Ihre Produktion zur Überwachung und Entscheidungsfindung.
Und da wir die Bedeutung der Besonderheiten kennen, ermöglicht Ihnen das System auch, sich in die Details eines bestimmten Auftrags, Artikels oder einer Ressource zu vertiefen, so dass Sie besser informiert sind und die optimalen Entscheidungen für Ihr Unternehmen treffen können.
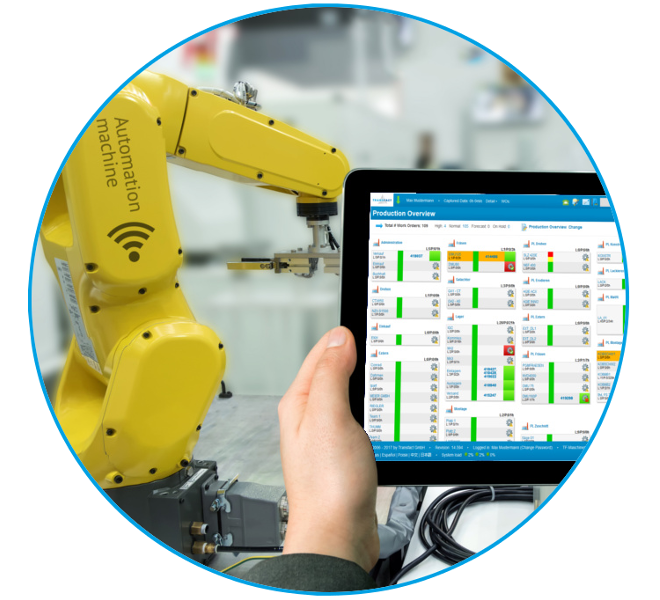

Ihre Artikeldaten im Zentrum
Alle relevanten Informationen zu einem Artikel leicht zur Hand.
Statistik und Historie der Lager- und Produktionsmengen auf einen Blick.
Alle Kosten und Preiskonditionen stehen in detaillierten und exportierbaren Übersichten zur Referenz und Pflege zur Verfügung.
Automatische Herstellungskostenberechnung mit detaillierten Aufschlüsselungen und historischen Daten.
Vollständig konfigurierbare Artikelparameter.

Arbeitspläne mit genau dem richtigen Detaillierungsgrad für Ihre Prozesse
Geben Sie Einrichtungszeiten, Ausführungszeit pro Charge, direkte Bedienerzeiten und sogar Wartezeiten für jeden Schritt an.
Automatisches Drucken von Dokumenten oder PDF-Berichten vor und/oder nach jedem Arbeitsschritt.
Definieren Sie die bevorzugten Ressourcen und erforderlichen Werkzeuge für jeden Arbeitsschritt.
Geben Sie zusätzliche Referenzdokumente und Anweisungen an, die bei jedem einzelnen Arbeitsschritt als Referenz angezeigt werden sollen.
Vollautomatische Revisionskontrolle für alle Arbeitspläne.

Konfigurierbare Fertigungsübersicht
Lassen Sie alle Ihre Produktionsbereiche in einer Ansicht anzeigen und erhalten Sie den Gesamtstatus der Produktion auf einem einzigen Bildschirm.
Ermöglichen Sie jedem Mitarbeiter, seine eigene Ansicht zu konfigurieren, um die Produktionsbereiche zu sehen, für die er verantwortlich ist.
Maschinenstatus, laufende Chargen, aktuell in Bearbeitung befindliche Artikel, geplante Gesamtproduktionszeiten für jeden Bereich und vieles mehr, alles direkt in Ihrer Übersicht.
Direkter Zugriff auf priorisierte Abarbeitungsliste für jede Ressource oder jeden Fertigungsbereich.
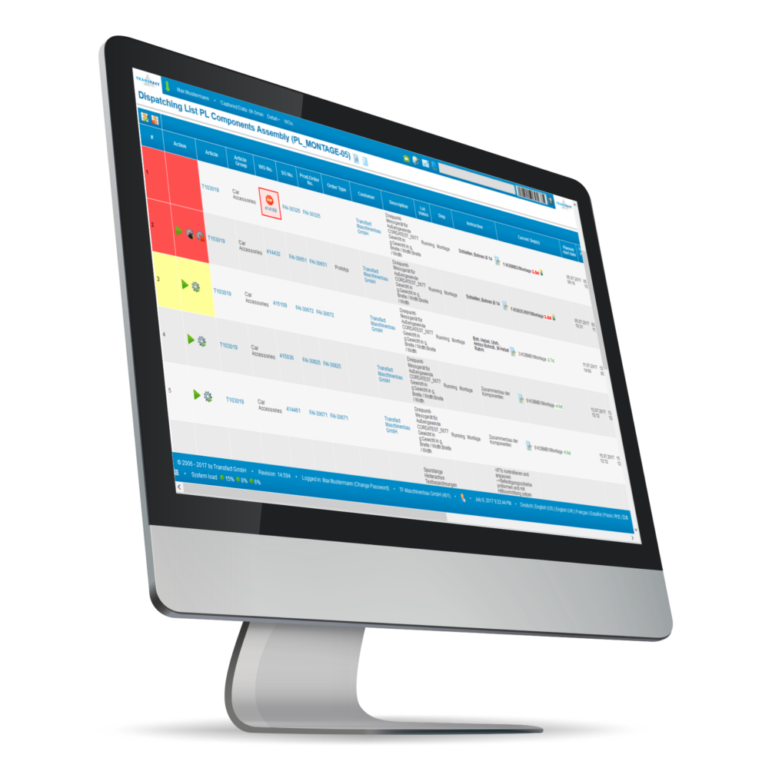
Priorisierte Abarbeitungslisten zeigen Ihnen den nächsten zu bearbeitenden Auftrag
Automatisch sortierte Abarbeitungslisten zeigen die Arbeitsaufträge an, die auf jeder Maschine, Ressource oder in jedem Fertigungsbereich zur Bearbeitung bereit sind.
Mit Hilfe von Farbcodes können Ihre Mitarbeiter Aufträge mit höherer Priorität, die sich verzögern oder bei denen die Gefahr einer Verzögerung besteht, schnell identifizieren.
Restzeiten, Liegezeiten und erwartete Fertigstellungszeiten werden vom System automatisch berechnet und angezeigt.
Berücksichtigen Sie mehrere Variablen für die automatische Sortierung der Dispatching-Listen, wie z.B.: Priorität, Verzögerung, geschätzte verbleibende Zeit und sogar individuelle Faktoren, die für jeden Artikel auf der Grundlage Ihrer Erfahrung festgelegt werden.

Sammeln Sie Ihre wertvollen Messdaten direkt im System
Integrieren Sie Kontrollmessungen in bestimmte Schritte Ihrer Arbeitspläne direkt im System.
Definieren Sie Messarten, erwartete Werte, Kontrollgrenzen und Stichprobengrößen für jede Messung.
Vollständige Revisionskontrolle der Prüfpläne.
Echtzeit-SPC-Datendiagramme, Berichte und Trenddiagramme mit einem Klick verfügbar.
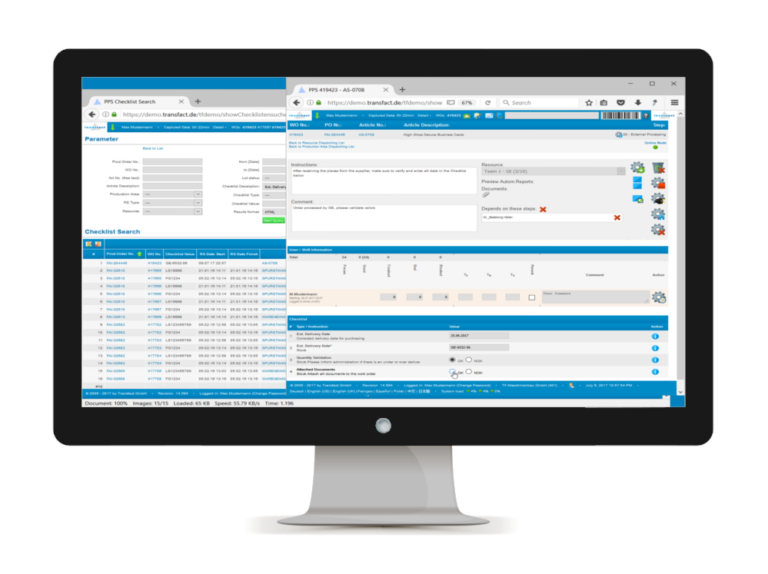
Checklisten zur Erleichterung der Sammlung von relevanten Prozessdaten
Sammeln Sie verschiedene Arten von Informationen zu einem bestimmten Schritt auf strukturierte Weise.
Definieren Sie Pflicht- oder Kannfelder für Ihre Mitarbeiter, um einen Schritt auszuführen.
Verwenden Sie den Checklistenbericht, um die verfolgten Informationen nach Datum, Produkt, Checklistentyp oder mit Hilfe einer allgemeinen Suche zu überprüfen.
Sie haben die volle Revisionskontrolle über Ihre Checklisten.
Automatische Funktionen bei bestimmten Schritten im Arbeitsplan auslösen.
Checklisten für automatische Funktionalitäten
Spezielle Checklistentypen ermöglichen es Ihnen auch, automatische Funktionalitäten zu aktivieren, wie z.B.: Hinzufügen eines vordefinierten Satzes von Nacharbeitsschritten, wenn eine bestimmte Prüfung fehlgeschlagen ist, oder Verwaltungsaufgaben wie das automatische Drucken der Liste von Komponenten, die aus dem Lager zu kommissionieren sind, bevor das Los in die Produktion geht.
Diese speziellen Funktionalitäten sind alle frei in jedem Arbeitsschritt konfigurierbar und ermöglichen es Ihnen, bestimmte Aktivitäten automatisch auszulösen, die sonst manuell durchgeführt werden müssten, wodurch Sie nützliche Zeit sparen.

Stücklisten mit integrierter Bestandsprüfung und Kostenberechnung
Verwalten und konfigurieren Sie alle Einheiten, die Sie benötigen.
Sie können alternative Komponenten und artikelspezifische Werkzeuge direkt aus der Stückliste bearbeiten.
Automatische Kommissionierung ab Lager für ausgewählte Komponenten.
One-Click Kostenberechnung für den gesamten Stücklistenbaum.
Integrierte Bestandsmengenprüfung für simulierte Mengen.
Vollautomatische Revisionskontrolle für alle Stücklisten.
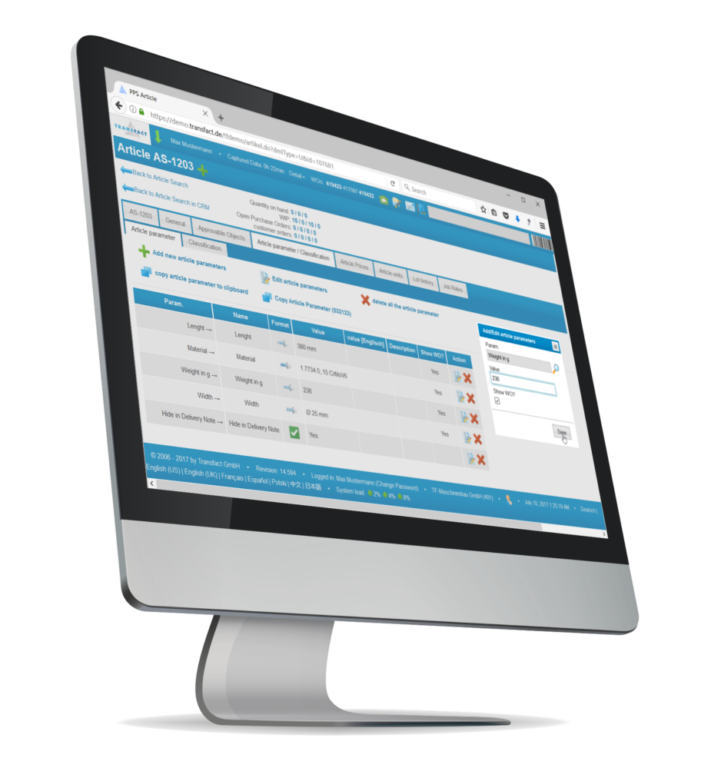
Leicht konfigurierbare und durchsuchbare Artikelparameter
Volle Kontrolle über die Suchkriterien, die zum Auffinden der Daten verwendet werden.
Einfach zu bedienen, schnell und leicht zu finden.
Suchen Sie Artikel nach Bereichen, Parametern, Status ihrer Stammdaten oder sogar nach bestimmten Kunden.
Wählen Sie die Informationen aus, die Sie in die Suchergebnisse aufnehmen möchten.
Kapazitätsplanung
Auf der Grundlage der Arbeitsplanzeiten, Mengen, WIP und Schichtplänen bietet Ihnen das System einen Überblick über die Auslastung jedes Produktionsbereichs oder sogar jeder geplanten Ressource.
Identifizieren und verwalten Sie Engpässe in Ihren Produktionslinien.
Einfache Umplanung von Arbeitsaufträgen und Neuzuweisung von Ressourcen.